SMT Manufacturing: Everything You Need to Know
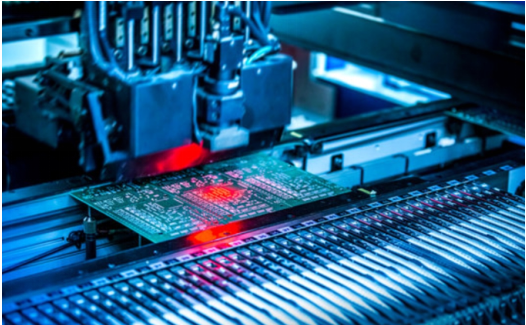
If you’re looking to get into small-machining technology, then this guide is for you. Written by an experienced engineer and manufacturer, this book covers everything you need to know about SMT manufacturing, from concept to practice. You’ll learn how to design and build small machines using custom-made parts, and how to troubleshoot and optimize your processes. With this book at your side, you’ll be able to make your own parts, products, and systems – and get started in small-machining technology today.
1. SMT Manufacturing: Everything You Need to Know
If you are in the electronics manufacturing business, you have probably heard of SMT manufacturing. SMT is short for Surface Mount Technology, and it is a process that is used to mount electronic components onto the surface of a circuit board. In this blog post, we will take a closer look at SMT manufacturing, and we will go over everything you need to know about this process.
The first thing to know about SMT manufacturing is that it is a highly automated process. In fact, most of the process is done by machines, and only a small amount of human intervention is required. This is different from the through-hole manufacturing process, which is still used for some electronic components, and which is a much more manual process.
The next thing to know about SMT manufacturing is that it is a very fast process. Once the circuit board is prepared, the component placement process can be completed in a matter of seconds. This is a big advantage over the through-hole manufacturing process, which can take minutes or even hours to complete.
Another advantage of SMT manufacturing is that it is a very precise process. The machines that are used for this process are able to place the components with a high degree of accuracy. This is important because it means that the circuit boards that are produced will have fewer defects.
Finally, it is important to know that SMT manufacturing is a very cost-effective process. This is because the machines that are used for this process are very expensive, and the process itself is very fast. This means that the cost per board is very low.
Overall, SMT manufacturing is a very efficient and cost-effective process. If you are in the electronics manufacturing business, it is definitely worth considering this process for your next project.
2. The Basics of SMT Manufacturing
In today’s market, there are many choices available when it comes to selecting a manufacturing process for your product. Among these choices, Surface Mount Technology (SMT) has become increasingly popular in recent years due to its many advantages. In this blog, we will take a closer look at SMT manufacturing and everything you need to know about this process.
What is Surface Mount Technology (SMT)?
Surface Mount Technology is a process that places electronic components onto the surface of a printed circuit board (PCB). This is in contrast to the through-hole method, which involves inserting components into drilled holes on the PCB.
SMT components are much smaller than through-hole components and can be placed much more densely on a PCB. This results in a smaller, more compact final product. In addition, SMT components are less likely to become loose over time and are less likely to be damaged during assembly and shipping.
The SMT process begins with a PCB that has been coated with a thin layer of solder paste. This paste acts as a adhesive to hold the components in place during the assembly process. The components are then placed on the PCB using a machine called a pick-and-place machine.
Once all of the components have been placed, the PCB is heated in a process called reflow soldering. This melts the solder paste and creates permanent connections between the components and the PCB.
Advantages of SMT Manufacturing
There are many advantages to using the SMT manufacturing process. As we mentioned before, SMT components are much smaller and can be placed much more densely on a PCB. This results in a smaller, more compact final product.
In addition, SMT components are less likely to become loose over time and are less likely to be damaged during assembly and shipping. The SMT process is also much faster than the through-hole process, which results in lower assembly costs.
Disadvantages of SMT Manufacturing
There are some disadvantages to using the SMT process as well. One of the biggest disadvantages is that SMT components are more difficult to repair and replace than through-hole components. This is because the connections between the components
3. The Benefits of SMT Manufacturing
The SMT process has many benefits that make it advantageous for manufacturers. Some of these benefits are listed below:
- Increased Efficiency
The SMT process is much more efficient than traditional manufacturing methods. This is because SMT machines can place components on a PCB much faster than human operators can. This increased efficiency leads to faster production times and lower production costs.
- Increased Accuracy
SMT machines are also much more accurate than human operators. This increased accuracy leads to less waste and fewer defects.
- Increased flexibility
SMT machines are very versatile and can be used to manufacture a wide variety of products. This increased flexibility allows manufacturers to respond quickly to changes in the market.
4. The Challenges of SMT Manufacturing
The surface-mount technology (SMT) process is a key step in the manufacturing of electronic devices and printed circuit boards (PCBs). SMT devices are small, lightweight, and low in cost, making them ideal for a wide range of applications.
However, the SMT process is not without its challenges. In this blog post, we’ll take a look at four of the biggest challenges faced by SMT manufacturers.
- Cost
The SMT process can be costly, especially when compared to traditional through-hole manufacturing. This is because SMT components are typically smaller and more intricate, which can lead to higher production costs.
- Quality
The SMT process can be difficult to control, which can lead to lower quality products. This is because the process is highly sensitive to temperature and humidity, and even the slightest variation can lead to problems.
- Yield
The SMT process can have a lower yield than traditional manufacturing processes. This means that more components may be rejected during the manufacturing process, which can lead to higher costs.
- Flexibility
The SMT process is not as flexible as traditional manufacturing processes. This means that it can be difficult to make changes to the design of products during the manufacturing process.
5. The Future of SMT Manufacturing
The surface-mount technology (SMT) process is constantly evolving. As new challenges and opportunities arise, the need for innovative solutions becomes more apparent. Here are five ways the SMT process could evolve in the future:
- Increased Use of Robotics
One way the SMT process could evolve is through the increased use of robotics. Robotics can help to improve efficiency and accuracy in the SMT process. Additionally, robotics can help to reduce the number of operator errors.
- Improved Materials
Another way the SMT process could evolve is through the use of improved materials. The development of new materials could help to improve the quality of the finished product. Additionally, new materials could help to reduce the cost of the manufacturing process.
- Improved Equipment
The use of improved equipment is another way the SMT process could evolve. The development of new equipment could help to improve the efficiency of the manufacturing process. Additionally, new equipment could help to reduce the cost of the manufacturing process.
- Improved Processes
The use of improved processes is another way the SMT process could evolve. The development of new processes could help to improve the quality of the finished product. Additionally, new processes could help to reduce the cost of the manufacturing process.
- Increased Use of Automation
The use of automation is another way the SMT process could evolve. Automation can help to improve the efficiency of the manufacturing process. Additionally, automation can help to reduce the number of operator errors.